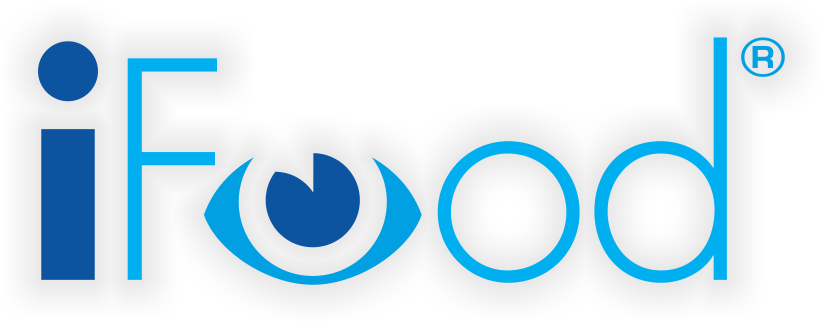
References
REFERENCE
GOSCH
From North Frisia to the whole Republic
GOSCH relies on iFood for transparency in production and trade
When Jürgen Gosch, a trained bricklayer, opened Germany’s northernmost fish stall in List in 1972, no one could have imagined how successful it would become. Today, the restaurants of the “Fish King of Sylt” can be found not only in their traditional maritime locations, but also on the cruise ships of TUI Cruises, as well as from Kiel to Munich and from Düsseldorf to Berlin, long since nationwide on the mainland. The hub for the 40 or so locations is the GOSCH factory in Ellingstedt, Schleswig-Holstein. In the modern production hall, not only up to 3 tons of fish are processed per day – also non-food articles, merchandising products and even glasses, tableware and the napkins for the restaurants are shipped from here to the entire country by the company’s own fleet of trucks. The iFood software solution from agmadata provides the necessary overview.
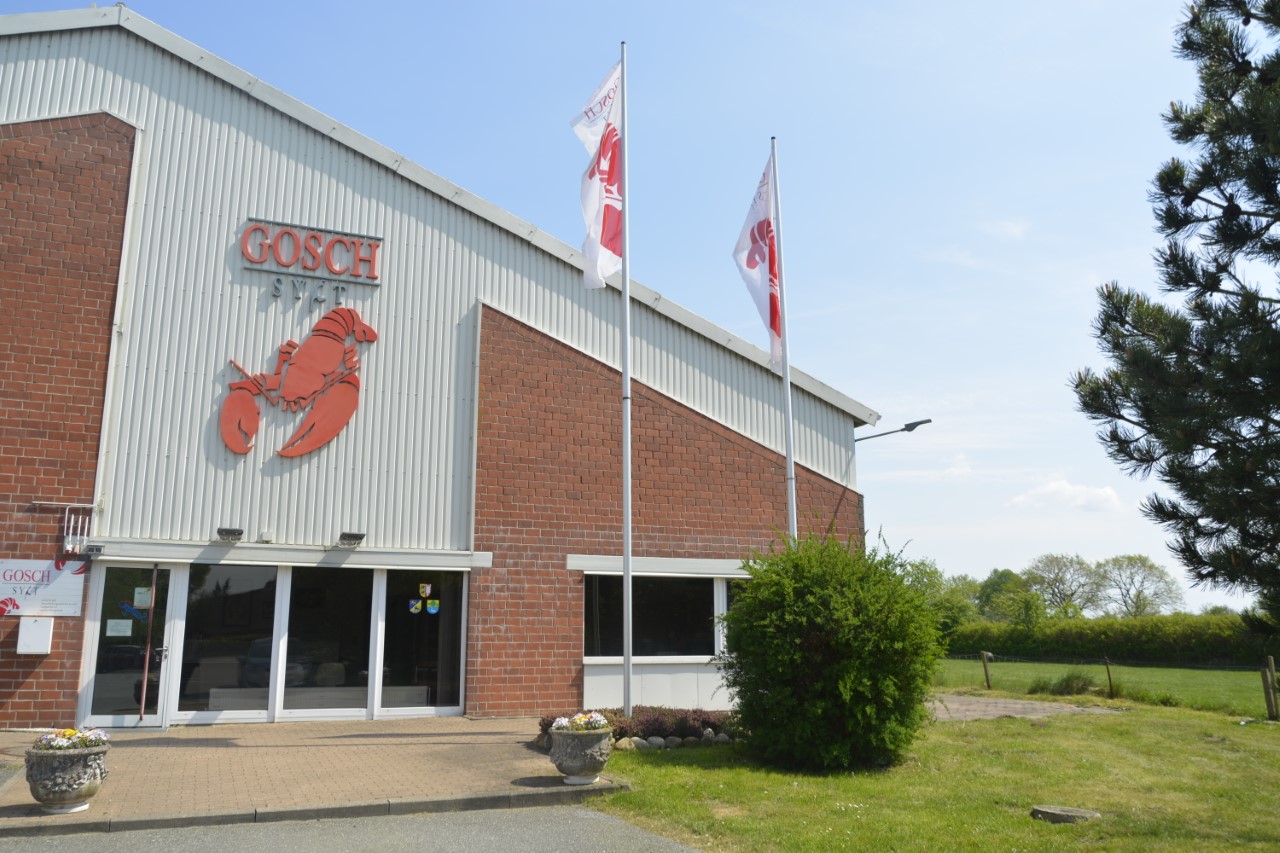
Ellingstedt, a small village near Schleswig with a population of just 800, is a tranquil place. Sheep graze around the production hall, the sun shines on the large forecourt of the manufactory and you almost think you can see the colorful market that regularly takes place here. But the first impression is deceptive – as soon as you enter the production, professional bustle dominates the scene. “In a way, we are a down-to-earth counterpart to the company’s headquarters on the fashionable island of Sylt,” says plant manager Friedrich-Wilhelm Kiy with a smile. “But that’s precisely why we need a highly professional organization, and for a long time now that can only be achieved with the appropriate IT support.”
The IT era at GOSCH began in the nineties with the DOS version of Navision. When a switch to Microsoft Dynamics became inevitable after the company was bought out by Microsoft in 2002, Kiy took the opportunity to look for a software solution that was better suited to the specific needs of the fishing industry. “At that time, it was already foreseeable that traceability would become our biggest challenge,” Kiy recalls. “That’s why we also chose agmadata, who had this theme down pat even back then.” With PYRAMODUL, GOSCH relied from then on on the leading enterprise resource planning system for the meat and fish industry. The existing article master data and inventories could be transferred to the new software thanks to appropriate import interfaces. Microsoft Dynamics was purchased as a supplement for accounting.
Fish is not a “standard
Nevertheless, the start with the new software should still cost the fish specialists some nerves. “The fact that agmadata was proficient in food traceability was, of course, an important prerequisite. But to use it, we first had to set up the system for us, from batch management to matching barcode labels,” recalls Kiy. “Fortunately, the manufacturer supported us to the best of their ability. With SAP, for example, we would have had to have everything completely reprogrammed – the price/performance ratio would never have been right for us.
However, the food specialists at agmadata did not manage entirely without reprogramming. The standard solution at that time did not yet cover all the specifics of the fish industry. In addition to the common article name, the genus and species names had to be stored in Latin, as well as other information such as the condition, catch areas or whether the fish originates from aquaculture or net fishing. This information is transferred to the goods receipt as a suggestion and can be adjusted there. Assigned quality management plans are used to record data for quality assurance and store it for supplier evaluation.
Over the years, numerous changes in the law have caused the catalog of requirements to grow and grow. Recently, calorie and nutritional information must also be stored in the article master in order to include them in the printout of labels for sales packaging. “Any normal merchandise management system would have been hopelessly overwhelmed by this flood of regulations,” Kiy knows. “agmadata has grown with the demands and has always delivered new versions on time to neatly meet the increased regulatory requirements.” Based on these positive experiences, it was easy for the manager to decide in 2012 to switch to the modern PYRAMODUL successor iFood, which runs entirely in the browser with Web 2.0 technology.
The right view for everyone
Since then, colleagues in the office and at external locations in particular have benefited from the new web interface. “iFood shows us much more information at a glance,” finds Kiy, although he has not yet used the graphical evaluations that have also become possible. “From a management perspective, it has become much easier to use. You don’t have to scroll as often now, you see everything in context and you can easily call up important additional information by simply clicking on it.”
The old, text-based interface continues to be used at the operational workstations. Indeed, in addition to the six PC terminals in the administration, Ellingstedt has two touchscreen consoles in production and four more in the warehouse. Seven handheld devices with built-in scanners and two scales with label printers are also connected. Four remote workstations on Sylt also work with the system and are mainly used for the separately managed merchandise management of the fish restaurants on the island.
Incidentally, the GOSCH locations order their requirements – from smoked eel, lobster and wine to souvenir plates, toilet paper or latex gloves – quite classically by fax. In the office, the orders are recorded and a picking slip is created, which summarizes the individual items according to their respective storage locations. In addition to cold and dry storage facilities, a frozen food warehouse with storage space management and the separate production warehouse in Ellingstedt, GOSCH also operates two external warehouses in Hamburg, where fish delivered in containers from overseas is temporarily stored until it is used.
All processes clearly defined
With so many warehouses and a good 1000 different items, it means avoiding unnecessary journeys. Clearly defined processes ensure this and the transparency required at Fisch. Thus, when assembling a delivery, employees only have to work through the already route-optimized sequence of the picking slip and scan the picked goods with the handheld device. This means that the actual quantities and batches are correctly recorded, the delivery bill is automatically printed in the office and the goods can be loaded onto one of the six trucks that make their daily journey to the Republic. On the way back from their tours, which usually last several days, they drive to the external container warehouses in Hamburg as required and bring the fresh goods they need back to Ellingstedt. There, the signed delivery receipts go back to the office, any corrections are taken over and the invoices are written. Finally, via an interface, the financial data is transferred to Microsoft Dynamics, which is responsible for accounting and payment control.
“The key thing for us is that we can tell where every single item is, where it’s going, and which delivery batch it came from,” Kiy explains. And not just for merchandise: iFood also provides comprehensive support for production. Thus, when a preparation is made, the removal of the ingredients from the production warehouse is recorded in the quantities specified by the recipe, the respective ingredient batches are recorded by handheld scan and documented under the newly assigned batch number. “Without any extra effort, we know for each bucket of garlic sauce exactly which spices from which manufacturer are in it with which batch,” Kiy is pleased to say.
The production manager also likes to rely on iFood when purchasing goods, for example, when he wants to know the latest purchase prices from various suppliers or, in the case of current contracts, when he has to ask how much has already been called off, what is currently on its way and what quantities are still open. And last but not least, merchandise management supports article maintenance when it comes to identifying those products for discontinuation that are only purchased in small quantities or by a small number of customers.
Conclusion: The right mix
After ten years of experience with agmadata software, Kiy’s summary is clear. “For us, the collaboration has definitely been worthwhile,” he emphasizes. “Even the standard software comprehensively covers the basic requirements of the fish industry. And for our various special requests, it has never taken more than a phone call and agmadata has responded.”
If he could wish for one thing, it would be: “That the legislator doesn’t bombard us with new requirements quite so often in the future. iFood takes the work out of it for us, but we’re starting to run out of space on the labels!”
agmadata has grown with the requirements and has always delivered new versions on time to neatly comply with the increased legal requirements.
For us, the collaboration was definitely worth it. Even the standard software comprehensively covers the basic requirements of the fish industry. And with our various special requests, it has never taken more than a phone call and agmadata has responded.